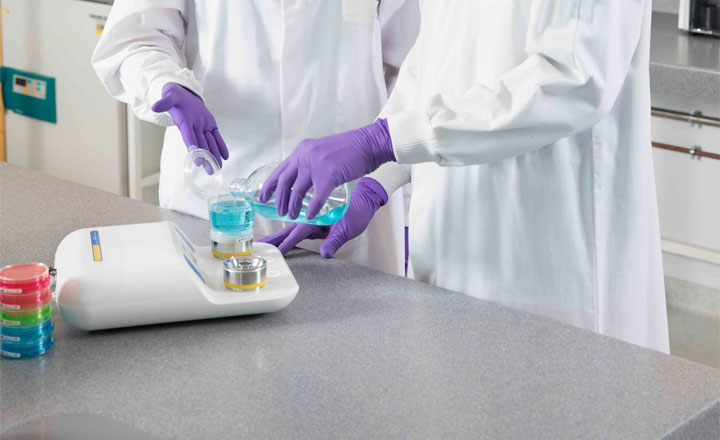
Introduction: The Milliflex Oasis® is the latest version of Merck's bioburden test. The changes are both visual and functional resulting in significant improvements to membrane filtration workflow. The new sleeker model has focused on better ergonomics for the end-user, improved traceability for both paper and paperless systems, and a cleaner more efficient process than anything else on the market.
In this interview, Michel van Musschenbroek, Field Marketing Manager at Merck, discusses with rapidmicrobiology how building relationships with customers can encourage feedback to improve the product and accredits its customers to be the driving force behind the company's innovations.
Q. How does Merck collaborate with customers to work on new technologies and solutions?
Michel: We don't just look to sell the product; we also look to support the product after the sale. What I mean by this, is through either field sales or marketing, we're continually communicating with our customers to understand what their issues are and how they might be addressed.
For instance, periodically, we do a 'voice of the customer', which consists of a short but comprehensive series of questions, that allows us to dive into the process of a particular test.
If the user is confident in our ability and desire to support them, they will give us valuable feedback. For example, someone might be experiencing some repetitive stress in the bioburden testing process and may have expressed this internally amongst but only amongst their work colleagues. But as they become more comfortable with our sales support, they are forthcoming with this information.
Through this relationship with the customer, we can get the 'whole picture' of the process from beginning to finish. This is where we continue to grow as a company and how customers influence the changes you see now with new products.
Q. What is the Milliflex Oasis® system & why do labs need it?
Michel: The Milliflex Oasis® system is the new product from the Milliflex® family and is the latest version of our bioburden testing system, which keeps our customers in compliance with their respective pharmacopoeia guidelines for bioburden.
The Milliflex Oasis® system can be used for bioburden in products or process water testing. In the lab, it’s typically used in a biosafety cabinet or laminar flow hood. Once set up, the pump can be linked to allow multiple Milliflex Oasis pumps to run simultaneously.
The pump is new this year, and it is phenomenal, with its sleek and lean design and easy-to-clean feature; that allows the user to perform sanitization themselves.
Typically, customers who don't use the Milliflex Oasis® system, have got a six-place manifold or they're putting filter cups on, having to disassemble it, autoclave it, and re-assemble. Our unit doesn't require any of that.
With our innovative design, we are looking to save time and reduce the risk of contamination. We wouldn't be aware of these issues if it weren't for our' voice of the customer' questionnaire, e.g. "What did you like? Well, we hated that we had to autoclave all the time" etc. So, we've developed a system that doesn't need autoclaving at all.
Q. The Milliflex Oasis® system has been around for four decades, why did you decide to update now?
Michel: The Milliflex Oasis® system is the new version in a series of models of the Milliflex® bioburden test and is a perfect example of how collaboration with the customer works.
Many of our users had an ergonomic challenge with the previous Milliflex® system, where it required the lab technician to press down on the funnel to sever it from the base of the membrane and break it apart.
Although this was an easy task for some, if you consider a lab technician working in a laminar flow hood, they may not have the leverage required to press down on the cup. Myself, I'm 200 pounds and six-feet tall, and it isn't a problem for me to press down, but someone shorter and lighter might find it difficult.
For the Milliflex Oasis® system, we looked at a completely novel way to remove that funnel body from the funnel system without any pressing down. This new version has solved that problem. It's now a simple matter of squeezing the funnel to remove it from the base, the membrane remains sealed to the base, and you can remove the funnel body without pressing down on it. This is probably the most significant change in the new system.
We also improved its sanitization process. We have an independently validated procedure which allows the user to sanitize the system once a month and avoid false positives.
Q. Which components stayed, and why?
Michel: Keeping our funnel integral to the funnel base remained. One of the notable differences between our product and others in the industry, is how our membrane is attached to the funnel base to avoid any chance of the sample bypassing it.
Upon completion of the filtration step, when you close the lid, you can verify the integrity of the membrane because you can see it is convex.
As it's convex, when you lay it onto the surface of the agar, it touches from the middle outwards to avoid trapping air bubbles, because you're pressing the air in the middle out, as opposed to rolling it or trying to lay it down flat. At no point of the filtration process are forceps required, helping to eliminate membrane handling.
Q. Which components did you change according to customers feedback?
Michel: Speaking with our customers, we found the process of transcribing work into lab workbooks for traceability was something that needed simplifying. First, we gave each of the standard media, i.e. TSA, SDA and R2A a different colour, so the end-user instantly knows exactly which media they are using.
Secondly, we put peel-able labels on the containers and on product packaging, which users can peel-off and put directly into their lab book. These labels have a barcode too, facilitating computerized data entry into a LIMS or Electronic Lab Notebook via a 2-D Scanner, which wasn't possible before.
The pump is now smaller and lighter, and therefore more aerodynamic, and its cleaner. It's cleaner because we have enabled the user to perform the sanitization themselves, without disassembling. By only running cleaning fluid through for 15 minutes, sanitizing the inside tubing and components, you can walk away and let it run on a lunch break. We have been able to show in an independent study that this cleaning process needs to be done only once a month, and there's no other system that allows you to do that.
There is also the check valve built-in to the unit to prevent backflow from the previous sample, which might cross-contaminate the current running sample. This extra layer of protection is needed as there is sometimes residual vacuum in the line. We've also included a drying-out step in the functioning of the pump, that allows you to release this vacuum without breaking the integrity of the membrane and funnel.
Q. How did Merck fill the gap between compendial and rapid testing?
Michel: The Milliflex Oasis® system is for the compendial test, but we also have a rapid microbial detection system called the Milliflex® Quantum system. This system allows you to interrupt the standard compendial test, add the reagent to the membrane, before rapid enumeration. Through an enzymatic reaction activated only by live organisms, it will provide you with a quantitative result of viable organisms under fluorescence much earlier than plates. In contrast, without this rapid step, colony development requires several more days.
In the event of a positive, you could put the filter back onto agar, finish your routine compendial test, and then, if necessary, perform an ID using any available ID system.
What's interesting about the Milliflex® Quantum system, is if you get positives in this test, their configuration on the membrane is a specific pattern. When you put the membrane back onto the agar and finish your compendial test, you'll see a like-for-like. The pattern of organisms grown after 24 hours is the same as the organisms that show up after three days. If you do see a positive with the Quantum, you don't need to finish the compendial bioburden test, unless you need to speciate.
Too often, people must displace their current system to bring in a rapid method. But if you have the Milliflex Oasis® system, you can piggyback the rapid (Milliflex® Quantum) system onto it.
Q. The Development of Milliflex Oasis® system was driven by customer feedback, what are labs saying now?
Michel: The product demos that I've performed have only received positive feedback. To quote one person, "you've answered every question and concern that we had with the previous version." It's very rewarding when we receive feedback telling us that we have been able to listen to the customer and apply those concerns into the product to satisfy the next generation. But who knows, maybe a couple of years down the road, we might find out from the customer, we could have done 'this' differently, and then that will be the next generation on.
But at this point right now, some of the biggest concerns were the traceability, transcribing errors, and the ability to remove the funnel cup. The change to the funnel cup is essential because it now has a hinged lid. While that doesn't seem like much, the previous version required the user to take the lid off and either hold it in their hand or place it on their workbench. Now the lid just gets opened, they pour their sample in, the lid comes down, because of this new hinge. So, we've kept the bench cleaner and still kept the same functionality. This is by understanding that the customer wants their bench to be as clean as possible because that's where they work all day. Such a small improvement like this has made people very happy.
Watch Promotional Video:
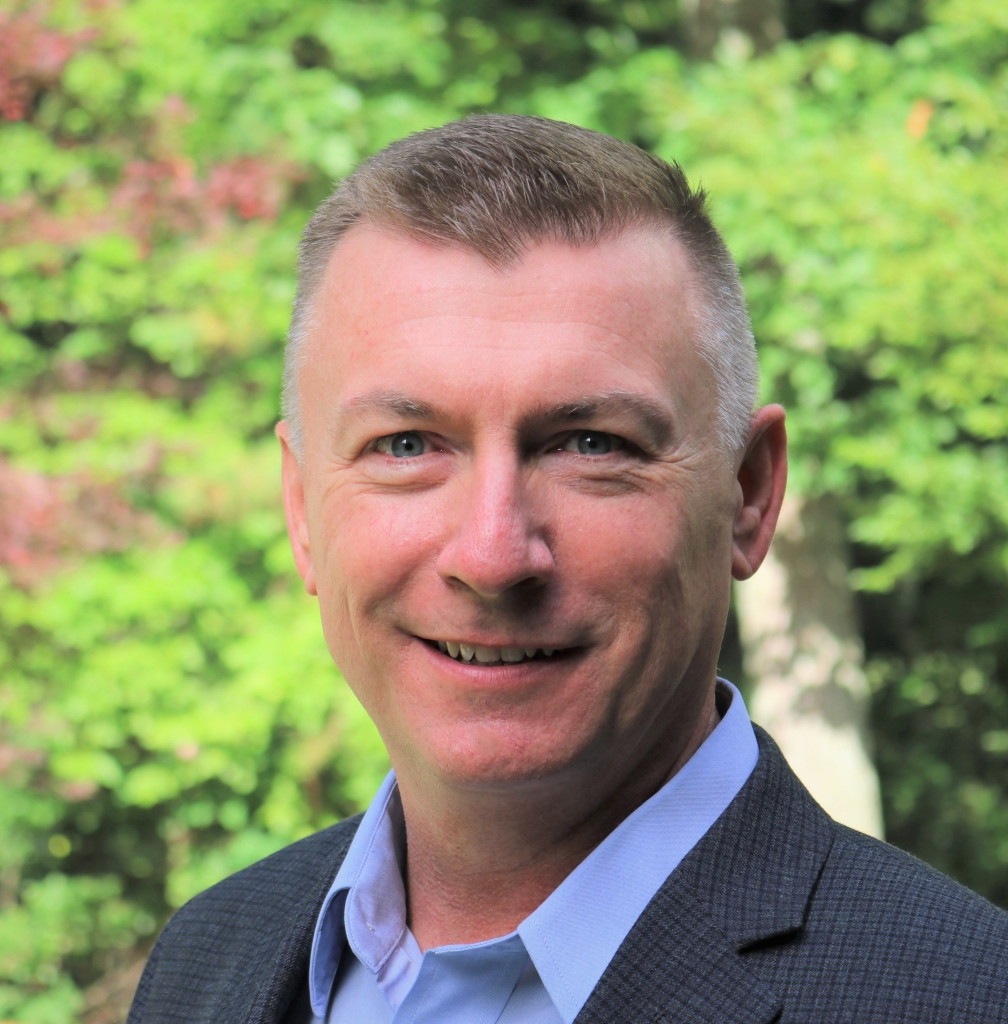
Michel van Musschenbroek Biography: Michel began work at Merck Canada 1989, and helped with its transition to the US 5 years later. In the US, he worked as tech support and inside sales rep at Merck in the BioMonitoring division, supporting the Food and Beverage industry. In 2000 he transferred to the field and in 2010 transitioned to the Pharmaceutical industry. In the Fall of 2019 he became a Field Marketing Manager